10-2. ENGINE ELECTRONIC CONTROL
MODULE (EECM). (cont.)
a. Test. (cont.)
(c) Move MASTER SWITCH to
START position.
The STARTER light should
come on.
Quickly increase function generator
frequency until STARTER and IGNITION lights
go off and FUEL light goes on. This should
happen between 1965 and 2059 Hz.
(d) Continue to increase function
generator frequency until READY TO LOAD
light comes on.
Should happen between 3287
and 3421 Hz.
(e) Set functional generator fre-
quency at 3500 Hz. Monitor fuel pump output
waveform on oscilloscope while tuning function
generator frequency between 3500 and 3000 Hz.
The waveform pulse width should vary inversely
proportional to frequency being applied and
be of an amplitude of 20-28 Vdc peak to peak
to 8-10 Vdc peak to peak.
NOTE
Disregard the leading edge spike on this
DC pulse. The vertical pulse shown on
the oscilloscope is the fuel pump off-
time. As the frequency is tuned between
3500 to 3000 Hz the vertical pulse will
also vary in width and height. The
highest voltage and pulse width will
occur at the highest frequency. This
indicates that the pump will be off
the greatest amount of time since
the EECM is reducing the fuel to the
turbine.
Inversely, the smallest pulse
will occur at the lower frequency when
the EECM is maximizing the fuel pump
on-time to increase the fuel to the
turbine.
(f) Move MASTER SWITCH to
OFF position. All lights should go off.
(g) Any discrepancy noted during
the above procedure indicates a failure in the
EECM pump control circuit. Refer to Table 2-4,
Malfunction 6.
b. Circuit Card Replacement.
(1) Removal.
(a) Place EECM so that bottom
cover faces up.
(b) Remove screws (1, figure 10-2),
washers (2), and bottom cover (3).
(c) Tag and disconnect connector
(4).
ARMY
TM 5-6115-612-34
MARINE CORPS
TM 6115-34/8
AIR FORCE
TO 36C2-3-471-2
NAVY
AG-320B0-MME-000
To prevent damage to jumper cable
(8), use care when removing circuit
cards.
(d) Remove screws (5) and lock-
washers (6).
(e) Carefully lift switch circuit card
(7) and disconnect jumper cable (8). Remove
card and jumper.
(f) Tag and disconnect connector
(9).
(g) Remove screws (10) and washers
(11).
(h) Remove spacer posts (12), micro-
processor circuit card (13), hex spacer posts (14),
and lockwashers (15).
(i) Tag and disconnect connector
(16).
(j) Remove screws (17), Iockwashers
(18), and power circuit card (19).
(k) Remove screws (20), Iockwashers
(21), hex spacer posts (22), and washers (23).
(2) Installation.
(a) Place Iockwashers (21) on screws
(20) and install in EECM.
(b) Place washers (23) on exposed
threads of screws (20). Add hex spacer posts (22)
and torque to 10-12 inch pounds (1.1-1.4 Nm).
(c) Position power circuit card (19)
on hex spacer posts (22) and secure with lock-
washers (18) and screws (17). Torque to 10-12
inch pounds (1.1-1.4 Nm).
(d) Insert connector (16) into power
circuit card.
(e) Place washers (11) on screws
(10) and install in EECM.
(f) Place
Iockwashers (15) on
exposed threads of screws (10). Add hex spacer
posts (14) and torque to 10-12 inch pounds
(1.1-1.4 Nm).
(g) Position microprocessor circuit
card (13) on hex spacer posts (14) and install hex
spacer posts (12).
(h) Insert connector (9) into micro-
processor circuit card.
Change 1
10-15
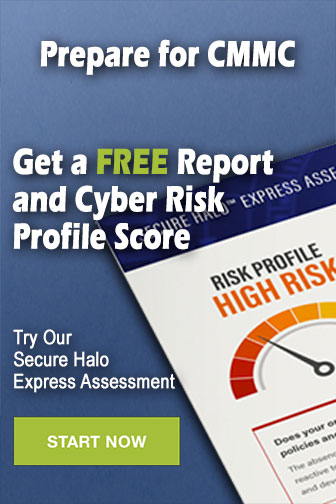