ARMY
MARINE CORPS
AIR FORCE
4-1.
PURPOSE
TM 5-6115-612-34
TM 6115-34/8
TO 35C2-3-471-2
AG-320BO-MME-OOO
AND FUNCTION
ELECTRICAL AND CONTROL SYSTEM.
b. Functional Desc ription. (cont)
(a)
0vertemperature.
generator temperature is monitored by
OF
DC
(cent)
The
a thermo
;witch mounted on the generator field winding. This
information is input to the GECM on JI pins D and F. If
the temperature exceeds 210 F (98.9 C), the switch
opens and a signals output on J2 pin O to the EECM.
The
EECM
will
turn
on
the
GENERATOR
OVERTEMP malfunction light and begin engine
shutdown.
(b) Overvoltage a nd Undervoltaae.
The output voltage is constantly monitored to ensure
that it is maintained within programmed limits. If output
voltage exceeds 35.5 volts and stays above this limit
for 0.75 seconds, the GECM will generate a fault
signal through J2 pin A to the EECM. The EECM
opens
the
output
contactor,
turns
on
the
GENERATOR OVERVOLTAGE indicator light, and
begins engine shutdown. if output voltage falls below
20 volts and stays below this limit for 0.75 seconds, the
GECM generates a fault signal through J2 pin B to the
EECM. The EECM opens the output contactor, turns
on the GENERATOR UNDERVOLTAGE indicator
light, and begins engine shutdown.
(c)
Overload Prot-
i
. The output
current is sensed by the 10OOA shunt located in the
negative (-) output circuit. As the load draws current
through the shunt, a voltage is developed between
pins C and D of the shunt. This voltage is input to the
circuit board on J2 pins J and K. If the load is drawing
more than 1070A, the board outputs a signal to the
EECM on J2 pin C. The EECM then turns on the
GENERATOR OVERLOAD malfunction light and
begins engine shutdown.
(4)
erv
Cha raing.
This
circuit
monitors battery voltage and supplies charging power
to the battery. The battery voltage is input to the
GECM on J3 pin Athroughthe 20A shunt. If the battery
charge is low, the charger, located on the GECM
board, s enabled. The charger receives power from
the generator on J1 pins G and H. The voltage is
regulated by the GECM and output to the battery at J3
pin A through the shunt. Current being drawn by the
battery causes a voltage drop across the shunt. This
drop is indicative of current and is shown on the
BAITERY CHARGING meter. The charging current is
also monitored by circuitry in the GECM and if
programmed limits are exceeded, the charger will be
disabled.
4-2. GENERATOR ELECTRONIC CONTROL
MODULE. Maintenance of the generator electronic
control module (GECM) consists of testing and
replacement of GECM components.
a.
Test Setup Procedure.
(1) Fabricate a GECM test fixture. An
illustration, parts list, and schematic, are provided in
Table 23. Table 41 lists additional equipment
required for GECM testing.
(2) Connect GECM to test fixture as
shown in Figure 4-1.
(3) Adjust test fixture switches and knobs
as follows:
~
SWITCH SETTING
SOURCE GEN/BATT
BAll_
METER SELECT
CHARGER VOLTS
RTD (5 POSITIONS)
2
OVERTEMP
ON
VOLTS ADJUST
FULL COUNTER
CLOCKWISE
FIELD
OFF
ENABLE
OFF
(4) Adjust power supply No. 1 to 28
(A 4) Vdc.
(5) Adjust power supply No. 2 to O Vdc.
(6) Adjust power supply No. 3 to 5
(A 0.5) Vdc.
(7) Adjust power supply No. 4 to O Vdc.
(8) Move ENABLE switch to ON position.
The UNDER VOLTS light should be on.
(9) Move SOURCE switch back to GEN
position.
b.
~haraer Voltaae Test.
(1)
Pedorm
test
setup
procedure
(paragraph 4-2a).
(2) Move SOURCE switch to GEN.
(3) Increase voltage from power supply
No. 2to 28 (*2) Vdc. The UNDER VOLTS light should
go off between 18to 18,7 Vdc. Reset GECM electronic
logic by moving SOURCE switch to BAIT position and
back to GEN position, Voltmeter on test fixture should
show between 28.6 to 29.6 Vdc. Record voltmeter
reading.
4-2
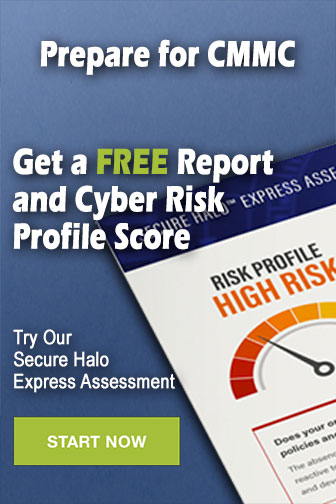