4-1
ARMY
TM 5-6115-612-34
MARINE CORPS TM 6115-34/8
AIR FORCE
TO 35C2-3-471-2
NAVY
AG-320BO-MME-OOO
CHAPTER 4
MAINTENANCE OF DC ELECTRICAL AND CONTROL SYSTEM
4-1.
PURPOSE AND FUNCTION OF DC
ELECTRICAL AND CONTROL SYSTEM. This
section gives a functional description
and maintenance procedures for the DC
electrical and control system.
The
system consists of the battery cable,
battery,
wiring harness
(W1),
slave
receptacle,
generator
electronic
control module (GECM), circuit breaker,
starter, and 20 amp current shunt.
a. Purpose.
The DC electrical and
control
system
provides
turbine
rotation
during
startup,
generator
output control and sensing, generator
protection, and battery charging.
b. Functional Description.
The
following is a simplified functional
description of the DC electrical and
control system.
The description is
keyed to the schematic in FO-5, TM
5-6115-612-12.
(1) Startup.
When
startup is
begun, 24 volts from the battery are
applied through the DC CIRCUIT BREAKER
(CB1) to the MASTER SWITCH. When the
MASTER SWITCH is placed in the RUN
position, the transfer pump will come
on and fill fuel filters.
When the
switch is placed in the START position,
the 24V signal is connected to the
engine electronic control module (EECM)
on the start circuit.
If the EECM has
not
detected
any
faults in
the
generator set,
it outputs the start
enable signal to the starter solenoid.
The solenoid energizes, supplies 24
volts
to the
starter
motor,
and
repositions
the actuator. As
the
starter motor begins
to turn, the
actuator causes the starter gear to
mesh
with
the
turbine
flywheel.
Turbine speed is sensed by the digital
speed sensor and relayed to the EECM.
When turbine speed reaches 60 percent
of maximum,
the EECM interrupts the
start
enable
power.
The solenoid
removes power from the starter and
retracts the starter gear from the
turbine flywheel.
(2) Generator Output Control and
Sensing.
generator
field-winding
power
and
provide
overtemperature
protection.
These functions are controlled and
monitored by the GECM and the EECM. If
the EECM does not sense a fault in the
generator set,
it enables the GECM via
the enable circuit on J4 pin F to the
GECM J2 pin L.
The GECM senses the
temperature
of the generator field
winding at J1 pin F.
If the temp-
erature is normal or below, field
winding power
is switched onto the
field positive (+) and negative (-)
lines (J1 pins C and B) to the gen-
erator.
The amount of field winding
power is adjusted by the GECM to main-
tain the output voltage level set by
the VOLTAGE ADJUST knob. The GECM
compares the output voltage setting at
J2 pin R with the remote voltage sense
at J2 pins E and F. If the two inputs
are different,
circuitry in the GECM
adjusts the field power until the
output voltage is correct.
(3)
Generator
Protection.
The
generator is protected
from
over-
temperature,
overvoltage,
under-
voltage,
and
overloading.
If any
condition exceeds programmed limits,
the GECM interrupts the field current
and sends a fault signal to the EECM.
When the EECM detects a fault, it turns
on
the
appropriate
MALFUNCTION
indicator light
and
starts
engine
shutdown.
The EECM will not permit
startup until the malfunction has been
corrected.
Each of
these conditions
is described below.
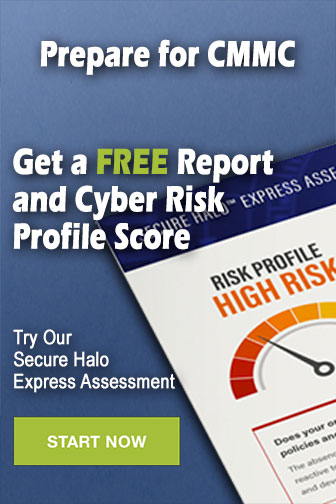