TM 5-6115-590-12
meter bracket from engine.
(2) Remove wiring harness leads from circuit
breaker (fig. 4-41).
(3) Remove attaching nut and washer from
bracket and remove circuit breaker.
b.
Installation.
(1) Install replacement circuit breaker in time
totalizing meter bracket. Secure with attaching washer
and nut.
(2) Connect wiring harness leads to circuit
breaker.
(3) Install time totalizing meter bracket in
engine bracket and secure with attaching washers and
screws. Tighten screws securely.
4-73.
Exhaust Gas Thermocouple
a.
Removal.
(1) Remove wiring harness leads from thermo-
couple (fig. 4-41). Note that chromel lead is matched to
CR marking and alumel lead is matched to AL marking.
(2) Remove two special attaching bolts and
washers and remove thermocouple from engine and
exhaust flange.
b.
Cleaning, Inspection, and Replacement.
(1) Clean thermocouple using an approved
solvent. Dry thoroughly with filtered compressed air.
(2) Visually inspect ceramic portion of thermo-
couple for cracks. If ceramic is cracked replace
thermocouple.
(3) Inspect terminals for security in ceramic and
for bending or damaged threads. If terminals fail to
meet inspection requirements and are damaged beyond
repair, replace thermocouple.
(4) Use a multimeter to check for continuity
between terminals. If there is no continuity, replace
thermocouple.
c.
Installation.
(1) Coat threads of special attaching bolts with
thin film of compound (Fel-Pro C-5).
(2) Install replacement thermocouple in engine
exhaust flange.
(3) Secure thermocouple with washers and
coated special attaching bolts. Tighten bolts to 50 to 75
inch-pound torque.
(4) Reconnect
wiring
harness
leads
to
thermocouple.
NOTE
Insure chromel lead is matched to CR
marking and alumel lead is matched to
AL marking.
4-74.
Engine Wire Harness
a.
Removal. Prior to removing the engine wiring
harness (fig. 4-41), tag or otherwise identify all
connectors, terminals and electrical leads, and note
routing and support clamp positions as an aid at
installation. Remove harness at connectors and
terminals.
b.
Cleaning and Inspection.
(1) Clean wiring harness assembly with filtered
compressed air or wipe with a clean rag moistened with
an approved cleaning solvent.
(2) Visually inspect for burned, bent, loose,
corroded or otherwise damaged connector pins and
terminals. Inspect wiring for breaks, loose connections,
or other obvious damage. Inspect insulation for burns,
chafing and deterioration. Report defects to direct
support maintenance for repair or replace defective
wiring harness.
c.
Test. Check continuity of wires using a multi-
meter or continuity light. Refer to figure 1-5 and FO-3
(located in back of manual) for wire routing. Continuity
must be indicated through individual wires.
d.
Installation. Install wiring harness assembly in
reverse order of removal.
4-75.
Fan Assembly, Oil Cooling
a.
Removal.
(1) Loosen clamp and remove end of hose
assembly from inlet flange of fan outlet flange and
remove ends of support assembly and hose assembly
from outlet flange of fan assembly, (fig. 4-43).
b.
Installation.
(1) Install replacement cooling fan assembly on
accessory gearcase using new packings.
(2) Secure fan assembly with attaching washers
and bolts. Tighten bolts to 50 to 70 inch- pound torque.
(3) Reconnect end of hose assembly and duct
support assembly to fan outlet flange. Tighten screws in
support assembly securely. Reconnect end of hose
assembly and clamp to fan inlet flange. Tighten clamp
securely.
4-76.
Fuel Control Assembly
a.
Removal.
(1) Remove wiring harness connector from fuel
solenoid and remove all tube assemblies from fuel
control assembly (fig. 4-43).
(2) Remove four attaching nuts and three
washers and carefully remove fuel control unit (fig. 4-44)
from engine in a straight line to avoid damaging the fuel
control drive shaft.
b.
Installation.
(1) Refer to figure 4-43 for orientation and
install replacement fuel control assembly. Insure that
fuel control drive shaft splines are properly meshed.
(2) Secure in place with attaching washers and
nuts. Tighten nuts to 50 to 70 inch-pounds torque.
4-97
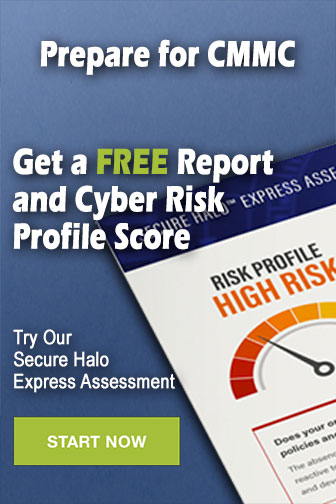