TM 5-6115-590-12
(3) Refer to figure 4-44 and reconnect all tube
assemblies to fuel control unit using new packings.
Connect wiring harness connector to fuel solenoid valve.
c.
Test.
(1) Connect fuel control assembly to engine
analyzer as shown in fig. 4-16 and check acceleration
limiter valve cracking pressure as follows.
(a) Disconnect fuel line from tee at fuel
control discharge pressure connection part, (fig. 4-16)
and install a 0 to 100 psig pressure gauge.
(b) Disconnect
control
air
line
at
acceleration limiter valve tee.
(c) With fuel supplied to fuel control
assembly at 15 psig, move master switch (S1) (fig.
2-11), sheet 1 of 2) on power unit instrument panel
assembly to START position and motor engine.
CAUTION
Do not exceed starter motor duty cycle.
(d) While motoring unit, check cracking
pressure. Cracking pressure should be 44 ± 1 psig. To
adjust, hold acceleration limiter valve adjustment screw
(fig. 4-16) on fuel control assembly and loosen locknut.
Adjust screw position using screwdriver and wrench
assembly (special tools). To increase cracking pressure
turn
acceleration
limiter
valve
adjustment
screw
clockwise. To decrease pressure, turn adjustment screw
counterclockwise.
CAUTION
Do not turn adjustment screw more
than three full turns in either direction.
(e) When satisfactory cracking pressure is
attained, tighten locknut.
(f)
Reconnect control air pressure line to
acceleration limiter valve. Remove gauge from tee on
fuel control assembly, reconnect fuel line, disconnect
and remove gas turbine engine analyzer.
(2) Check fuel control governor speed setting
as follows:
(a) Connect gas turbine engine analyzer to
power unit as described in paragraph 4-14b. Use tach-
generator rpm gauge (fig. 4-14) on analyzer panel to
check engine speed.
(b) Start engine (fig. 2-11) and accelerate
to no load governed speed. Operate at this speed for
approximately two minutes to stabilize operation.
(c) Apply full load to engine. To apply load,
open compressed air outlet as described in fig. 2-18 and
operate cooled air system as described in fig. 2-15.
(d) With engine operating at full load, tach-
generator rpm gauge (fig. 4-14) should read 4150 ± 10
rpm (equal to an engine spec of 40,700 ± 100 rpm).
(e) If tach-generator rpm gauge does not
read 4150 ± 10 rpm use screwdriver and wrench
assembly (special tools) to adjust full load governed
speed.
(f)
Hold governor adjustment screw (fig. 4-
16) on fuel control assembly and loosen locknut. Turn
governor adjustment screw clockwise to increase full
load governed speed, and counterclockwise to decrease
full load governed speed. When adjustment is
satisfactory, tighten locknut.
CAUTION
Do not turn screw more than three
turns in either direction.
(g) Close
compressed
air
outlet
as
described in fig. 2-18, shut off cooled air system as
described in fig. 2-15, and return the engine to no load
governed speed.
(h) Tach-generator rpm gauge (fig. 4-14)
should read 4242 rpm (maximum) (equal to an engine
speed of 41,600 rpm).
(i)
If tach-generator rpm gauge does not
read 4242 rpm (maximum), use screwdriver and wrench
assembly (special tools)to adjust no load governed
speed setting.
(j)
Hold governor adjustment screw (fig.
4-16)
on fuel control assembly and loosen locknut.
Turn adjustment screw clockwise to increase no load
governed turn adjustment screw counterclockwise to
decrease no load governed speed.
(k) When adjustment is satisfactory, tighten
locknut, disconnect and remove gas turbine engine
analyzer.
4-77. Fuel Control Unit Filter
a.
Removal. Without removing the fuel control
unit from the engine, unscrew filter cap as shown in
figure 4-45 and remove and discard filter element and
packings.
b.
Cleaning and Inspection.
(1) Wash filter cap with an approved cleaning
solvent and dry thoroughly with filtered compressed air.
(2) Visually
inspect
filter
cap
for
cracks,
corrosion, damaged threads or other signs of obvious
damage. Replace filter cap if found to be damaged.
c.
Installation. Install replacement filter element
and new packings in reverse order of removal. Tighten
filter cap securely but do not overtorque.
4-78. Engine Fuel Filter Element
a.
Removal. Without removing the engine fuel
filter assembly (fig. 4-44) from power unit, unscrew filter
case from filter assembly as shown in figure 4-45.
Remove and discard filter element, packing and gasket.
4-98
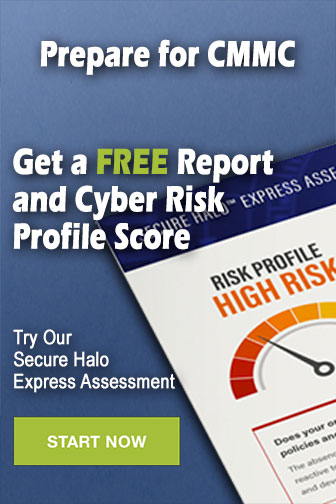