ARMY
TM 5-6115-612-34
MARINE CORPS TM 6115-34/8
AIR FORCE
TO 35C2-3-471-2
NAVY
AG-320B0-MME-000
10-1.
PURPOSE AND FUNCTION OF ENGINE
AND GENERATOR CONTROLS AND INSTRU-
MENTS. (cont)
b. Functional Theory of Operation.
(cont)
(6) Battery
charging
monitor.
The control
panel
BATTERY CHARGING
meter allows the operator to see that
the generator set batteries are being
charged while the engine is running.
Signal lines are routed directly to the
control panel
and connected to the
BATTERY CHARGING ammeter.
(7) Status monitoring
and
con-
trol. Both engine and generator status
are monitored by the EECM while the
engine is running and the generator is
supplying power.
If a malfunction is
detected, the EECM either attempts to
correct the problem or automatically
removes power from the contactor (if
the contactor is energized) and shuts
down the engine.
To make these deci-
sions, the EECM microprocessor monitors
the engine monopole speed sensor, EGT
thermocouple,
and oil pressure.
For
the generator,
the EECM microprocessor
monitors the overload,
undervoltage,
overvoltage,
and temperature status via
signals sent to it from the GECM. A
detected
fault is
monitored
for
three-fourths of a second to see if it
corrects
itself
before
the
microprocessor software program takes
any
action.
In general,
with the
exception of a minor overspeed con-
dition,
any detected fault results in
display of the fault on one of the
control
panel
MALFUNCTION
lamps,
removal of
starting
power to the
aircraft by a disabling of the con-
tactor relay, and an automatic shutdown
of the engine.
(a) Engine fault detection and
shutdown.
An engine fault consists of
an overspeed, overtemperature, or low
oil pressure condition.
Overspeed is
monitored via the speed signal line to
the EECM, overtemperature is monitored
via the EGT line to the EECM, and oil
pressure is monitored via the oil
pressure and signal line to the EECM.
The only fault that does not cause an
immediate
shutdown is an
overspeed
condition between 100 and 109 percent
of
full
rated
engine
speed. If
frequency of pulses on the speed signal
line indicates such a condition, fuel
flow to the engine is decreased as
discussed.
If speed increases above
109 percent, or any of the other three
possible
faults
occur,
the micro-
processor
initiates an
automatic
shutdown routine.
First,
the micro-
processor disables the contactor to
prevent current from flowing to the
aircraft being started.
This is done
by disabling the contactor enable line
from the microprocessor to the con-
tactor gate and buffer on the switch
card.
This switches the gate output to
disable the contactor relay driver and
disable the output contactor signal.
When this occurs, the generator set
contactor relay deenergizes to remove
power from the aircraft.
Deenergizing
the contactor relay also removes +24
Vdc from the control panel CONTACTOR
CLOSED lamp,
turning it off. At the
same time,
the microprocessor places
one or more signals on
the status/
control
output
lines to the switch
circuit card.
Regardless of where the
fault lies, the generator enable signal
is always disabled which turns off the
lamp driver circuit. The READY TO LOAD
line is thereby disabled, turning out
the READY TO LOAD lamp and stopping the
HOURMETER.
Other signals
are
also
output on any one of the status control
lines to indicate where the fault is
occurring.
If the fault is determined
10-6
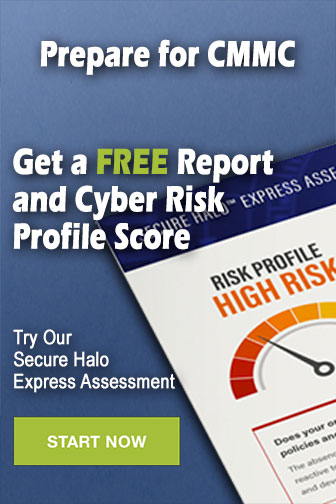