1 0 - 1.
PURPOSE AND FUNCTION OF ENGINE
AND GENERATOR CONTROLS AND INSTRU-
MENTS. (cont)
b. Functional Theory of
Operation.
(cont)
microprocessor.
Drive is
converted
into an analog signal that controls a
pulse width modulator.
If the speed
value is too high, the drive signal is
decreased and the pulse width modu-
lation output duty cycle decreases.
(4)
Contactor
enabling
Con-
tactor enabling is the process by which
generated power
is supplied to the
load.
As the engine continues to
accelerate, its speed is monitored by
the EECM microprocessor until
100
percent speed is reached.
The fact
that 100 percent speed has been reached
is determined by the microprocessor
which compares a stored value for 100
percent speed with the actual value on
the speed signal line. When that point
is reached, the engine is turning the
generator at a rate where the generator
power output is sufficient to supply
the load (start the aircraft). At 100
percent
power,
the
microprocessor
outputs a level on one of the four
status/control
lines to the switch
card.
After buffering, this becomes
the generator
enable
signal
which
actuates a
lamp
driver
circuit.
Generator enable is also sent off the
card through connector P4 to the GECM
to enable the GECM to control the
generator.
The lamp driver generates
the ready to load signal that is routed
from the EECN to the control panel
causing the READY TO LOAD lamp to come
on. When the operator sees the READY TO
LOAD lamp come on, he places the
CONTACTOR switch momentarily in the
CLOSED position,
then releases it back
to the normal center position.
This
places +24 Vdc on the (Contactor On)
line to the switch card where it is
ARMY
TM 5-6115-612-34
MARINE CORPS TM 6115-34/8
AIR FORCE
TO 35C2-3-471-2
NAVY
AG-320B0-MME-000
shaped, then used to set a latch on the
switch circuit card.
The set output of
the latch is applied to a contactor
gate and buffer where it is gated with
a contactor enable output that the
microprocessor generates at this time.
The resulting gate output drives a
contactor relay driver which in turn
outputs an enabling contactor enable
level.
After
routing
this
signal
through and out of the control panel
unaltered,
it becomes the contactor
enable level to the output contactor.
This level
energizes
the contactor
relay, allowing power to flow from the
generator through the closed contactor
relay contacts to the aircraft being
started.
To show the operator that the
relay is closed, closure of another set
of relay contacts applies
+24 Vdc
through control panel terminal board
TB1 to the CONTACTOR CLOSED lamp. The
lamp
comes on
to verify that the
contactor relay is energized.
(5) Output
power
control.
The
operator can monitor the voltage and
current being supplied to the air-
craft.
He is also able to regulate the
voltage
output of
the
generator.
Voltage is displayed on the control
panel VOLTAGE meter, while current is
shown on the OUTPUT CURRENT meter.
Output voltage is controlled by turning
the control panel VOLTAGE ADJUST knob.
The changing
resistance
caused
by
turning the knob is routed to the GECM
to regulate
the generator
voltage
adjust level.
The operator adjusts the
knob while watching the VOLTAGE meter
until the meter reading is correct.
Additionally,
the HOURMETER is con-
nected across the VOLTAGE meter so that
it accumulates the number of hours that
voltage has been generated by the
generator set.
10-5
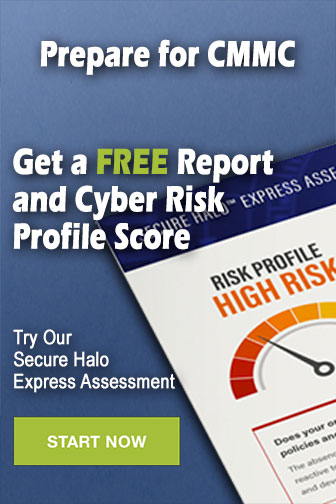