ARMY
TM 5-6115-612-34
MARINE CORPS TM 6115-34/8
AIR FORCE
TO 35C2-3-471-2
NAVY
A G - 3 2 0 B 0 - M M E - 0 00
10-1.
PURPOSE AND FUNCTION OF ENGINE
AND GENERATOR CONTROLS AND INSTRU-
MENTS. (cont)
b. Functional Theory of Operation.
(cont)
valve signal line to the engine.
Fuel
valve signal being in this state opens
the engine fuel valve and allows fuel
to flow to the engine in preparation
for startup.
Next,
the EECM micro-
processor software places a series of
pulses on
the drive
output
to a
digital-to-analog converter.
Conver-
sion of
the digital
microprocessor
output to an analog signal is necessary
for compatibility with inputs required
by a pulse width modulator. The level
of the resulting analog signal from the
converter
causes
the
pulse
width
modulator
to output
a duty-cycle-
varying square wave on the fuel pump
drive line to the engine. For startup,
the duty cycle is set at a fixed level
to drive the fuel pump at the rate
necessary to supply fuel to the engine
so that it can be started.
(c) Status monitoring/automatic
shutdown.
Five
seconds
after
the
starter
signal is
generated,
the
microprocessor
program
samples
the
speed signal line to count pulses from
the monopole speed sensor. At the same
time,
it monitors the EGT line.
The
rate of the pulses on the speed signal
line should indicate that the engine
has reached 10 percent of full oper-
ating
speed.
If not,
the micro-
processor
starts a
shutoff routine,
because it is assumed that the engine
is not running properly or has not
started. If
all
indications
are
normal, no
action is taken by the
microprocessor
and
the
engine is
allowed to accelerate.
If, however, an
abnormal speed or temperature condition
is
sensed,
the automatic
shutdown
sequence is
entered.
This routine
first disables the ignition and starter
outputs from the microprocessor which
in turn disable the starter signal and
igniter drive signals to the engine.
The microprocessor
next
outputs a
signal to the switch circuit card on
one of the status/control lines.
After
buffering, this signal on the valve
enable line is applied to a driver that
disables the fuel valve signal line to
the engine.
This shuts off fuel flow
to the engine to keep it from starting.
(d) Completion of
startup
sequence.
The
EECM
microprocessor
continues to
monitor
engine
speed
during stratup.
When 60 percent speed
is sensed,
the ignition enable and
starter enable lines to the switch
circuit card are disabled, shutting off
ignition
and
starter levels to the
engine.
The engine is considered to be
successfully started and is now allowed
to accelerate by itself.
(e) Fuel
flow control.
The
EECM controls fuel flow to the engine
at all times after startup to ensure
that the proper amount of fuel is
flowing.
It makes adjustments to the
fuel
flow as
necessary to provide
optimum fuel delivery regardless of
fuel temperature, viscosity, or load.
To determine proper flow, the micro-
processor monitors the speed signal
line and counts the rate at which
pulses occur.
This rate is compared to
values
stored in the microprocessor
that represent ideal speeds for the
engine
at various times during its
acceleration.
If the measured pulse
rate over time does not compare to the
ideal
speed/time
rate,
the
micop-
rocessor
adjusts
fuel
feed ac-
cordingly.
This is
accomplished
through
the drive output from the
1 0 - 4
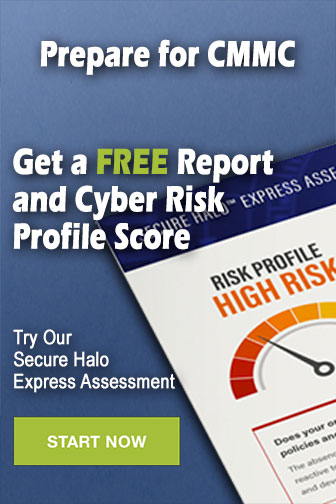