ARMY
T M 5 - 6 1 1 5 - 6 1 2 - 3 4
MARINE CORPS TM 6115-34/8
AIR FORCE
TO 35C2-3-471-2
NAVY
AG-320B0-MME-000
1 0 - 1.
PURPOSE AND FUNCTION OF ENGINE
AND GENERATOR CONTROLS AND
INSTRU-
MENTS. (cont)
Functional Theory of 0peration.
(cont)
b.
transformer,
an ac voltage is induced
at the transformer output and applied
to rectifier/filter circuitry.
After
rectification of the ac, it is filtered
to supply both +12 Vdc and -12 Vdc
levels to EECM circuits and also fed
back to the control circuitry. If the
voltage level on the +5 Vdc output line
increases above about 6.2 volts, the
crowbar
control
line
passes
this
voltage to the crowbar control cir-
cuit.
In response, the crowbar trips,
shorting the prime input lines to-
gether. The resulting short across the
+24 Vdc prime power line causes the
control panel circuit breaker to trip
and remove power from the generator set.
(2) Initial
power
application.
Refer to FO-9, sheet 2. The DC CIRCUIT
BREAKER on the control panel controls
application of +24 volt battery power
from the battery to the control panel
and the EECM.
Input prime power from
the battery enters the control panel
through TB1, passes through the CIRCUIT
BREAKER (when closed), and is dis-
tributed on the panel. When the PANEL
LIGHTS switch is closed, the two panel
illumination lamps receive the +24 Vdc
and are lighted. Prime power is also
placed on the center pole of the MASTER
SWITCH and CONTACTOR switch. Addition-
ally,
it passes through the battery
line to the EECM where it is connected
to the center pole of one set of relay
contacts.
To apply power to the EECM
circuits,
the
operator
places
the
MASTER SWITCH in the RUN position. This
places power on the +24 Vdc line from
the control panel to the EECM. In the
EECM, this voltage is distributed to
various
EECM circuits
is
also
applied
to the power
supply circuit
card.
This supply in turn generates +5
Vdc and ~12 Vdc levels to power EECM
logic
and the microprocessor
as ex-
plained in paragraph 10-1b(1) above.
The microprocessor on the micro-
processor circuit card is the control-
ling and decision-making device for the
entire engine
and generator
controls
and instruments.
Stored within it is
the software program that controls
exactly how and in what sequence events
are to happen that lead up to engine
start and contactor enable.
It also
monitors
various
status
lines to
determine if faults have occurred, and
makes decisions as to whether or not
the generator set should be shut down -.
if the fault occurs.
When the micro-
processor receives operating power on
the +5 Vdc line from the power supply
card, it enters a startup sequence that
eventually leads to engine ignition and
startup.
The first step in the startup
sequence sets the fault output from the
microprocessor.
This level is buffered
and sent to the switch circuit card
where it is applied to a relay driver
and a set of eight latches.
In the
latches,
the fault level causes any
latch input to be routed directly to a
corresponding
latch
output
without
being
altered.
The
microprocessor
begins to monitor the speed signal from
the monopole speed sensor
signal from the exhaust gas temperature
(EGT) thermocouple.
The speed signal
consists of a series of pulses from the
monopole speed
sensor such that more
pulses are received when the engine is
turning faster and vice versa.
Any
pulses on the speed signal line are
clipped by the digital-to-TTL shifter
so that output pulse levels from the
shifter are compatible with TTL logic
levels required by the microprocessor.
1 0 - 2
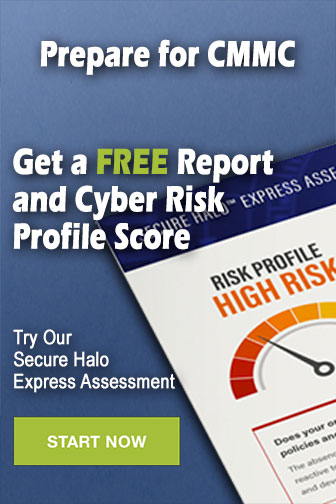