TM 5-6115-590-12
temperature sensing and control in MUST hospital
elements that do not utilize the return air ducts. When
remote temperature sensing is not used, a plug with a
jumper wire must be plugged into the receptacle on the
return air inlet panel.
(1) Cooled Air System (fig. 1-8, 1-9). The cooled
air system uses two independent 10 ton (refrigerating
capacity) refrigeration systems for maximum flexibility
of operation. The two refrigeration systems may be
operated individually or together to provide 20 tons
cooling capacity. Each refrigeration system is a vapor
cycle closed loop system consisting of an electric-motor-
driven refrigerant compressor, two condenser cooling
fans, a refrigerant receiver, an expansion valve, an
evaporator, two recirculating fans, a refrigeration
solenoid valve, a compressor bypass solenoid valve, an
overpressure switch, a refrigeration de-icing system, and
associated tubing, fittings and refrigerant level sight
gages. All electric motors in the refrigeration system are
powered by the 400 Hz electrical system and all control
components are powered by the 24V DC electrical
system. Output temperature control of the refrigeration
systems is automatic with variable adjustment provided.
Refrigeration output temperature control is accom-
plished by three solenoid-operated valves, a refrigerant
flow control valve, a compressor bypass valve, and a
de-icing
valve.
The
de-icing
system
functions
automatically to prevent ice formation on the evaporator
core.
(2) Heated Air System (fig. 1-10). The heated air
system uses two independent control and mixing
systems connected to a single source of heated air.
Each system uses hot compressed air from the gas
turbine engine compressor through the engine load
control valve. The heated compressed air passes
through
one
or
both
thermostatically
controlled,
electrically actuated flow control valves into the mixing
chambers. The heated air is mixed with recirculating air
from the recirculating fans and is distributed through the
air outlet ducts to the elements of the MUST hospital.
Output temperature control of the heated air system is
automatic with variable adjustment provided. The
temperature sensors, installed in the return air inlets,
provide automatic temperature control of the output air
to the selected temperature by opening and closing the
flow control valves to increase or decrease the flow of
heated compressed air to the mixing chambers.
Overtemperature thermoswitches installed in the mixing
chambers, will actuate to close the engine load control
valve in the event heated air temperatures exceed safe
maximum.
(3) Ventilating Air System. The ventilating air
system provides for the circulation of air without the
addition of heated or cooled air. The system uses the
recirculating fans and ducts in the refrigeration systems
and heated air systems to circulate ambient temperature
air through the other elements of the MUST hospital.
Vent openings in the return air inlet panel may be
opened as required to admit make-up air.
e. Water System (fig. 1-11 and 1-12). The water
system, when provided with an external supply of water
will deliver hot and cold water under pressure to other
elements of the MUST hospital. The water system
includes a cold water pump, hot water pump, exhaust-
gas-to-water heat exchanger, exhaust gas flow control
valve, hot water storage tank, pressure (surge) tank,
pressure relief valves, check valves, pressure and
temperature control switches, and interconnecting lines
and fittings. The cold water pump receives inlet water
and delivers the water to the cold water outlet and to the
hot water heat exchanger. A surge tank is connected to
the cold water system to prevent the noise and effects
of water hammer and cycling. The water is heated in
the heat exchanger and goes to the hot water storage
tank. The hot water pump draws water from the storage
tank and delivers it under pressure to the hot water
outlet. Pressure switches are utilized to activate the hot
and cold water pumps as required to maintain a
constant water pressure in the system. A hot water
temperature switch controls the positioning of the
exhaust gas flow control valve to regulate the flow of
exhaust gas to the heat exchanger and maintain a
constant water temperature. Temperature and pressure
relief valves in the water system protect the system
from damage due to excessive temperature and/or
pressure. A thermostatic switch in the water tank
compartment is used to control a solenoid valve to
bleed hot compressed air from the engine compressor
into the water tank compartment to prevent freezing
during low temperature periods of operation. Drain
fittings are provided to completely drain the water
system during periods of inoperation.
f. Compressed Air System (fig. 1-10 and 1-13). The
compressed air system consists of various ducts,
valves, and controls utilized to deliver compressed air
from the gas turbine engine compressor to the heated
air system, water tank compartment, engine air cleaner
ejector, vacuum system eductor, and for external
pneumatic power requirements. Compressed air to the
heated air system is bled off through the engine load
control valve which is modulated by a load control
thermostat m the engine exhaust to prevent the engine
from
being
overloaded
by
excessive
shaft
and
pneumatic loads. Compressed air to the engine air
1-14
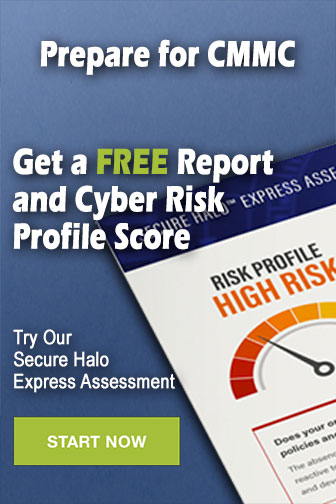