TM 5-6115-590-12
Section XII. Maintenance of Compressed Air and Vacuum System
4-48. General
The compressed air and vacuum system provides
compressed air and vacuum for external applications
and compressed air for scavening the engine air inlet
filter and for heating the water storage compartment.
These systems consist of control valves, tube and hose
assemblies, vacuum ejector and exhaust ducts.
4-49. Tube Assemblies and Plumbing Fittings
a. Compressed Air System.
(1) General. The hose and tube
assemblies
and
plumbing
fittings
provide
interconnection of the compressed air system.
(2) Removal. Remove hose and tube
assemblies and plumbing fittings as required for
replacement following the sequence of index numbers
on fig. 4-30.
(3) Cleaning, Inspection and Repair.
(a) Clean hose and tube assemblies
and plumbing fittings with an approved cleaning solvent
and dry thoroughly with filtered compressed air.
(b) Inspect all threaded parts for
stripped, crossed or peened threads. If threads are
damaged beyond repair, replace the damaged part.
(c) Inspect hose assemblies for
cracks,. breaks, chafing and damage to hose interior. If
damaged, replace hose assembly.
(d) Inspect tube assemblies for kinks,
bends, cracks, or other damage which might restrict flow
or result in leakage. Inspect nuts and sleeves on tube
assemblies for loose sleeves or damage to nuts. If
damaged, replace tube assemblies.
(e) Inspect plumbing fittings for
cracks or clogged passages. Clean clogged passages
and replace cracked fittings.
(f) Replace all gaskets and packings
if removed regardless of condition.
(4) Installation. Install hose and tube
assemblies and plumbing fittings in reverse order of
removal procedures and sequence of index numbers
assigned to figure 4-30.
b. Vacuum System.
(1)
General.
The
hose
and
tube
assemblies
and
plumbing
fittings
provide
interconnection of vacuum system components.
(2) Removal. Remove hose and tube
assemblies and plumbing fittings as required in the
sequence of index numbers assigned to figure 4-31.
(3) Cleaning, Inspection and Repair.
(a) Clean hose and tube assemblies
and plumbing fittings using an approved cleaning
solvent and dry thoroughly with filtered compressed air.
(b) Inspect all threaded parts for
stripped, crossed or peened threads. If threads are
damaged beyond repair, replace the damaged part.
(c) Inspect hose assemblies for
cracks, breaks, chafing and damage to hose interior. If
damaged, replace hose assembly.
(d) Inspect tube assemblies for kinks,
bends, cracks or other damage which might restrict flow
or result in leakage. Inspect nuts and sleeves on tube
assemblies for loose sleeves or damaged nuts. If
damaged, replace tube assemblies.
(e) Inspect plumbing fittings for
cracks or clogged passages. Clean clogged passages
and replace cracked or damaged fittings.
(f) Replace all gaskets and packings
if removed regardless of condition.
(4) Installation. Install hose and tube
assemblies and plumbing fittings in reverse order of
removal procedures and sequence of index numbers
assigned to figure 4-31.
4-50. Compressed Air and Vacuum System
Components
a. Removal. Disconnect plumbing connections to
each component as required. Remove attaching
hardware and remove component to be replaced
following the sequence of index numbers assigned to
figure 4-30 and 4-31.
b. Cleaning, Inspection and Repair
(1) Clean components with an approved
cleaning solvent and dry thoroughly with filtered
compressed air.
(2) Inspect threaded areas for crossed,
stripped, or peened threads. If threads are damaged
beyond repair, replace components in reverse order of
removal.
Section XIII. Maintenance of Engine and Skid Assembly
4-51. General
The engine and skid assembly contains the gas turbine
engine, the upper and lower electrical power chassis, oil
and fuel tanks, fuel boost pump, fuel filter and fuel float
tank. Access to the engine and skid assembly for
replacement of components is obtained by removing the
access panels as shown in figure 4-32. Before
removing the access panel to the fuel and oil
components, the electrical connectors to the main
instrument panel must be disconnected.
4-75
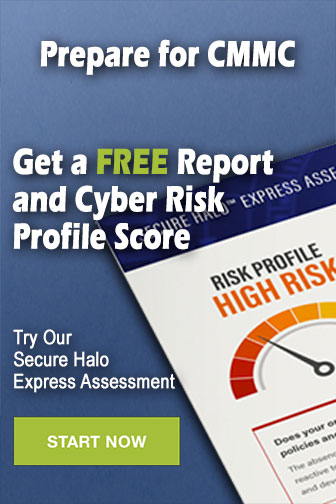