TM 5-6115-590-12
(2) Start engine and accelerate to no load
governed
speed.
Operate
at
this
speed
for
approximately two minutes to stabilize operation.
(3) Operate both heated air systems at full
heat as described in figure 2-16.
(4) With heated air systems operating at full
heat, place the mode select switch to COOL on both
systems. The heated air flow control valves will remain
open but the engine load control valve will close. Open
the engine load control valve by installing a jumper
between analyzer jacks identified LOAD VALVE and DC
POWER. This condition bypasses the over temperature
thermo switches in the air out compartment and delivers
both cooled and heated air at the same time to provide
sufficient engine load to raise the exhaust gas
temperature to 10750F (5520C to 5790C), shut down
power unit and thermostat setting.
CAUTION
Monitor the air out temperature and
shut down the power plant if air
discharge temperature exceeds 2000F
(930C).
(5)
Observe
engine
exhaust
gas
temperature on analyzer. The load control thermostat
should modulate the load control valve to control exhaust
gas temperature at 10250F to 1075°F (5520C to 5790C).
If control temperature is not 10250F to U 10750F (5520C
to 5790C), shut down power unit and adjust thermostat
as follows.
(6) Remove thermostat by holding flats on
thermostat valve with a wrench and remove tube
assembly.
(7) Remove one attaching bolt and washer,
retainer plate and shim washers. Remove thermostat
from turbine plenum flange. Remove thermostat valve
from body.
(8) Measure total thickness of shims with
micrometer. To decrease temperature setting. increase
shim stack thickness. To increase temperature setting,
decrease shim stack thickness. A change of 0. 001 inch
in shim stack thickness will change cracking temperature
by approximately 300F. Add or remove shims as
required. Install corrected thickness of shims and fitting
(9) Reinstall thermostat in reverse order of
removal.
(10) Recheck controlling temperature at
least twice.
(11) When controlling temperature is
satisfactory, shut down power plant and disconnect and
remove analyzer.
4-47. Flow Control Valve
a. Removal. Remove wiring harness connector
from flow control valve (fig. 4-29) Loosen clamps on
each side of valve, remove clamps from flange and
remove valve and gasket.
b. Installation. Install valve in place using new
gaskets
in
reverse
order
of
removal
procedures
Reconnect wiring harness connector.
1.
Nut
2.
Flat washer
30.
Pressure cap assy
58.
O-ring
86.
Pressure cap assy
3.
Bolt
31.
Union
59.
Tube assembly
87.
Nipple
4.
Bolt
32.
Tube assembly
60.
Tube assembly
88.
Pressure, switch
5.
Loop clamp
33.
Tube assembly
61.
Tube assembly
89.
Tee
6.
Bracket
34.
Elbow
62.
Tee
90.
Nipple
7.
Tube assembly
35.
Nut
63.
Tube assembly
91.
Tee
8.
Tube assembly
36.
O-ring
64.
Tube assembly
92.
Tube assembly
9.
Nipple
37.
Tube assembly
65.
Tube assembly
93.
Union
10.
Pressure relief valve
38.
Nut
66.
Tee
94.
O-ring
11.
Tube assembly
39.
Bolt
67.
Tube assembly
95.
Surge tank
12.
Sleeving
40.
Flat washer
68.
Reducer
96.
Hose clamp
13.
Tube assembly
41.
Lock washer
69.
O-ring
97.
Tube assembly
14.
Tube assembly
42.
Plug valve
70.
Bolt
98.
Grommet
15.
Nut
43.
Tube assembly
71.
Flat washer
99.
Nipple
16.
Elbow
44.
Nut
72.
Lock washer
100.
Relief valve
17.
Reducer
45.
Cap assembly
73.
Cold water pump
101.
Elbow
18.
Union
46.
Union
74.
Nut
102.
Nut
19.
O-ring
47.
Ball valve
75.
Flat washer
103.
O-ring
20.
Tee
48.
Cap assembly
76.
Hot water pump
104.
Bushing
21.
Nut
49.
Tube assembly
77.
Nipple
105.
O-ring
22.
Union
50.
Nut
78.
Gate valve
106.
Thermostatic switch
23.
Tube assembly
51.
Bushing
79.
Nipple
107.
Check valve
24.
Nut
52.
Packing
80.
Elbow
108.
Tube assembly
25.
Union
53.
Union
81.
Stand pipe
109.
Tee
26.
Nut
54.
Check valve
82.
Tube assembly
110.
Tube assembly
27.
Tube assembly
55.
Tube assembly
83.
Tube assembly
111.
Bolt
28.
Tube assembly
56.
Elbow
84.
Nut
112.
Flat washer
29.
Nut
57.
Nut
85.
Union
113.
Hot water tank
IDENTIFICATION KEY TO FIGURE 4-26 (PAGE 468, 469, 470)
Change 7 4-71
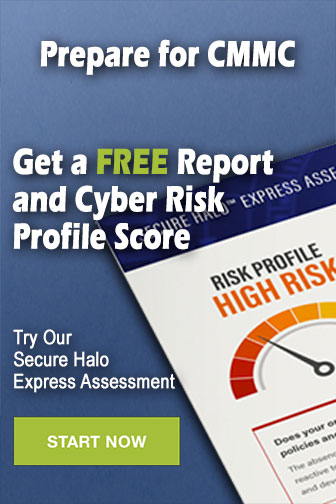