ARMY
TM 5-6115-612-34
NAVY
AG-320B0-MME-000
c Requirements.
(1)
Equipment. An approved metalizing gun
designed to provide automatic gas pressure and wirer
feed control.
(2)
Coating materials.
(a)
Bond coat Shall be an approved
martensitic chromium corrosion resistant steel or a nickel
aluminum composite wire (item 11, appx B)
(b)
Coating alloy Shall be an approved
aluminum alloy wire (item 14, appx B)
(c)
Resin sealer coat (Item 105, appx B)
d
Procedure
WARNING
Toxic solvent Is used for general cleaning Illness or
skin
damage
may
be
caused
by
prolonged
breathing of solvent fumes or excessive skin
contact with the liquid Ensure there is adequate
ventilation and avoid open flame or sparks when
using flammable solvent
(1)
Cleaning Parts shall be thoroughly cleaned
free from grease, oil, dirt, or other foreign materials by
vapor degreasing or by washing In petroleum solvent
(item 5, appx B) or other suitable solvent
(2)
Masking Parts shall be masked as required
to protect areas not designated to be coated Masks may
be steel, brass, or other suitable materials properly
protected against adherence of the sprayed coating
(3)
Surface conditioning Grit blast the masked
parts sufficiently to remove all metallic luster, excessive
blasting snail be avoided
(a)
Care
must
be
taken
to
prevent
contamination of the prepared surfaces by contact or
other means. If necessary to handle the prepared part,
clean, lint-free gloves (Item 6, appx B) must be used
Parts shall be spray coated as soon as possible, but In
no case longer than 2 hours after surfaces have been
prepared for coating If this time is exceeded, repeat step
(3)
(b)
Wipe grit blasted surfaces with clean,
lint-free rag (item 7, appx B) dampened with acetone
(item 1, appx B) or other suitable solvent just prior to
spraying
(4)
Spray coating.
(a)
Place part in fixture designed to permit
uniform coverage of areas designated to be coated
(b)
Preheat the cleaned and masked parts
to 175-200° F (79-93° C)
(c)
Apply the bond coat onto designated
areas to a thickness of 0 002-0 007 in (0.05-0 18 mm)
(d)
As soon as spraying operations are
started, introduce a stream of air onto the part being
coated to maintain a part temperature 120-250° F (40-
121° C) Maintain cooling air blast throughout all coating
operations.
(e)
Spray the aluminum alloy (item 14,
appx B) coating onto the designated areas to a total
thickness sufficient to meet drawing requirements after
finish machining.
(f)
The spray coating must impinge on the
surface to be coated at an angle of 75-105 degrees
(1.31-1.83 radians)
(g)
Remove masking in a manner that will
avoid damage to the sprayed coating
(h)
Impregnate the aluminum alloy coating
completely with an approved silicone resin coating (item
15, appx B) Completely impregnation is accomplished
when, 30 minutes after application, resin is still present
on the coated surfaces Bake the silicone resin coated
part by heating to 140-160° F (60-73° C) holding at heat
for 25 to 30 minutes, heating to 440-460° F (226-238°
C), holding at heat for 55 to 65 minutes, heating to 575-
625° F (301-331 o C) and holding at heat for 165 to 195
min- utes, and cooling In air to room temperature
e
QualityThe sprayed coating shall be adherent to
the basis material and shall have a uniform surface free
from blisters, chips, or other objectionable imperfections
not readily removable by finishing operations.
(1)
Examination shall show the coatings to be
free from cracks and massive oxides, and contamination
at the interface between the coating and substrate.
(2)
Quadrant cases Hairline cracking of the
coating at the permanent (non-disassembled) split line is
acceptable provided there is no evidence of bond
separation
Change 4 14-7
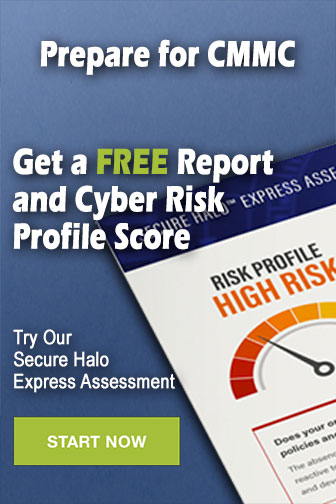