ARMY
TM 5-6115-612-34
NAVY
AG-320B0-MME-000
(b)
Preheat cleaned and masked part to
175-200° F (79-93° C) using plasma, flame, or oven
Check temperature with infrared thermometer gun or
equivalent
(c)
Spray
the
molybdenum
powder coating (Item 78, appx B) onto designated
surfaces to a thickness required by engineering drawing
(d)
The molybdenum spray must impinge
on the surface to be coated at an angle of 75-105
degrees (1 31-1 83 radians)
(e)
Remove masking In a manner as will
avoid damage to the sprayed coating
(f)
The part number,
serial
number,
coating thickness, date sprayed and any discrepancies
noted during the coating process must be recorded when
the parts being processed are serialized parts.
(g)
Coated areas shall be rotary wire
brushed to remove any loose particles on the surface
and edges of coating
e
Molybdenum Removal. If required, the sprayed
molybdenum coat may be removed by masking areas
not coated and removing plasma sprayed molybdenum
by grit blasting using 120 grit aluminum oxide at 60 to 80
lb (414 to 552 kPa) air pressure or other methods
approved by Materials Research and Engineering.
f
Quality Perform In-process inspection as follows
(1)
Parts and coupons shall be inspected for
adequate surface preparation and cleanliness just prior
to coating.
(2)
The sprayed coating shall be adherent to
the base material and shall have a uniform surface free
from blisters, chips, or other objectionable imperfections.
(3)
Metallographic
examination
The
lest
specimen shall be metallographically examined at 100
diameters for the following
(a)
Freedom of cracks
(b)
Freedom from separations within
the coating or between the coating and the base metal
(4)
Coating thickness. The coating thickness
shall be measured for conformance to drawing
requirements
(5)
Hardness Surface hardness shall be not
lower than 81 0 HR30T Surface on which hardness is
determined should have 0.003-0 005 In (0 076-0 127
mm) removed by machining or polishing to provide a
smooth surface.
(6)
Minimum bond strength shall be 2500 psi
(172 kPa)A bond test specimen will be checked on Initial
production startup and on request thereafter
g
Approval To assure adequate performance
characteristics, parts sprayed In accordance with this
specification shall be approved by Quality Assurance
unless such approval Is waived.
h
Rejection Parts on which the sprayed coating
does not conform to the requirements of this
specification, or to authorized modifications, shall be
subject to rejection
i
Approved Equipment The following equip- ment
Is approved for use under requirements of this
specification
D-6 Flame Spray Coating - Aluminum Alloy (4043).
a
Scope
(1)
Type
This
specification
covers
the
procedure for flame spray deposition of an aluminum
alloy
(2)
Application Primarily to provide abradable
coating to reduce clearance between compressor rotor
blade tips and sealed compressor case wall
b
Applicable Documents The latest Issue of
Aerospace Material Specifications (AMS) shall apply
(1)
Engineering Material Specifications
Nickel-aluminum composite (item 11,
appx B)
Steel wire, corrosion resistant (item 12,
appx B)
(2)
Engineering Process Specifications
Vapor degreasing (item 4, appx B)
Grit blasting (Item 3, appx B)
Solvent, petroleum (item 5, appx B)
Aluminum alloy wire (Item 14, appx B)
14-6 Change 4
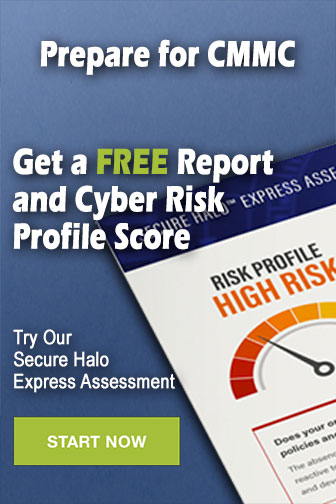