ARMY
TM 5-6115-612-34
MARINE CORPS TM 6115-34/8
AIR FORCE
TO 35C2-3-471-2
NAVY
AG-320BO-MME-OOO
6-3.
ELECTRICAL HIGH PRESSURE FUEL
PUMP.
Maintenance of the electrical
high pressure fuel pump (figure 6-3)
consists of testing and repair.
a.
Test.
(1) Remove
electrical
high
pressure fuel pump in accordance with
paragraph 4-41a, TM 5-6115-612-12.
(2) Connect pump in test setup as
shown in figure 6-4.
(3) Open valves (3) and (6).
(4) Apply sufficient voltage to
pump (7) to provide 50 psi reading on
gage (4).
Flowmeter (5) should show
fuel flow greater than 46 PPH and
voltage should be less than 12 Vdc.
(5) Apply sufficient voltage to
pump (7) to provide 200 psi reading on
gage (4).
Flowmeter (5) should show
fuel flow greater than 67 PPH and
voltage should be less than 24 Vdc.
CAUTION
To prevent damage, do not allow
pump
to operate in
deadhead
condition for extended period of
time.
Immediately
reduce
pressure
when
gage
reads in
excess of 320 psi.
(6) Turn off power to pump (7)
and close valve (6).
Apply 12 Vdc to
pump.
Gage (4) should show pressure in
excess of 320 psi.
Immediately reduce
voltage to pump or open valve (6) to
prevent pump
from
operating
under
deadhead condition for extended length
of time.
(7) Secure from test.
If flow-
meter and/or pre
incorrect, pump
repaired or repl
6-4
ssure gage readings
is faulty and shoul
aced.
are
d be
b.
Electric Motor Disassembly.
(1) Match mark both end bells
with housing.
CAUTION
To prevent damage, maintenance on
the electric motor shall be done
on a clean, well-lighted surface.
(2) Remove plug (1, figure 6-5)
and contact brush (2).
(3) Remove screws (3) and lift
off rear end bell (4).
(4) Remove spring shim (5), solid
shim set (6),
and bearing cover (7).
Set aside and keep in correct order.
(5) Match mark front end bell (8)
with pump (9).
(6) Remove screws (10) to discon-
nect pump from front end bell. Pump is
not repairable.
(7) Remove end bell and coupling
(8.1).
(8) Carefully
remove
armature
(13) from motor stator (12).
(9) Using an arbor press and
V-notched wedge,
remove ball bearings
(14) and (15).
Ensure that edges of
wedge bear against inner race of
bearing.
(10) Remove deflector (16) and
shim set (17).
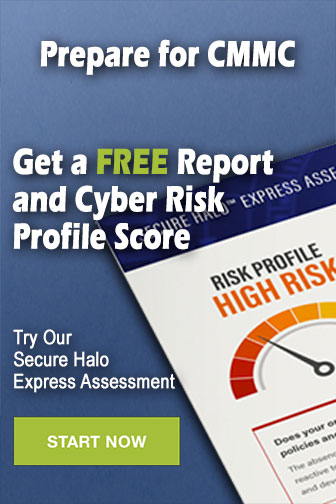