TM 5-6115-590-12
connection provisions on the enclosure provide mobility
of the unit by truck, railroad car, helicopter, airplane,
mobilizing transporter wheels, and by skidding.
b. Gas turbine engine power plant (fig. 1-3). The
gas turbine engine power plant is installed in the lower
left front corner of the power unit and consists of a
pneumatic and shaft power gas turbine engine, 60 Hz
and 400 Hz generators, a fuel system, a lubrication
system,
various
air
ducts,
plumbing
installation,
electrical wiring installation, and a skid base. Two
electrical rack assemblies are installed on the power
plant skid base and contain various regulating and
control components for the power unit electrical system.
The gas turbine engine power plant provides shaft
power to drive the 60 Hz and 400 Hz generators.
Compressed air from the engine compressor section is
used for external pneumatic power requirements, for
heated air in the conditioned air system, water
compartment heating air, vacuum system eductor air,
engine air cleaner ejector air and deicing the engine air
inlet filter. The engine exhaust heat is utilized through a
heat exchanger to heat water for the water system.
(1) Pneumatic and Shaft Power Gas Turbine
Engine (fig. 1-3). The gas turbine engine is a self
contained power source and requires only a fuel supply
and electrical starting power to maintain a constant
output power and rpm (revolutions per minute). Engine
power is developed through compression of ambient air
by a two-stage centrifugal compressor; the compressed
air, mixed with fuel and ignited, drives a radial inward-
flow turbine wheel. The rotating shaft power of the
turbine wheel drives the compressor, the accessories,
and the output drive shafts. A portion of the
compressed air developed by the compressor is
available for external pneumatic power applications. An
internal system of pneumatic and electro-mechanical
controls provide automatic and coordinated control of
engine starts, acceleration, and operation. A minimum
of additional external controls are required to initiate the
engine starting cycle, monitor engine operation, and to
stop engine operation. The gas turbine engine consists
of a compressor and turbine section, accessory drive
section, fuel control system, bleedair control system,
engine electrical system, and engine lubrication system.
(a) Compressor and Turbine Section. The compressor
and turbine section is the power nucleus of the engine.
The two stage centrifugal compressor develops
compressed air for fuel combustion and for external
pneumatic power. The single stage turbine incorporates
a single combustion chamber which mixes compressed
air with the fuel spray from the fuel atomizer, ignites the
fuel-air mixture and directs.
the products of combustion to the turbine wheel. The
turbine wheel converts the power developed in the
combustion chamber to shaft power which drives the
compressor impellers and the accessory drive section.
(b) Accessory Drive Section. The accessory drive
section is a reduction gear system which reduces the
high rotational speeds developed by the turbine wheel to
a usable rpm to drive the engine accessory gear box
and a dual pad gear box for the 60 Hz and 400 Hz
generators. In addition to mounting pads for the two
generators, the accessory drive section provides
mounting pads and drive gear connection for the
following accessories oil pump assembly; fuel control
unit, centrifugal switch assembly; cooling air fan; starter
motor; and tachometer-generator.
(c) Fuel System (fig. 1-4). The engine fuel system
consists of components which function automatically to
regulate fuel flow to the combustion chamber and
maintain near constant governed speed and safe
operating temperatures under varying conditions of
starting, acceleration, and load application. Control
components function by sensing engine speed, turbine
exhaust gas temperature and compressor air pressure,
and react by adjusting fuel flow to maintain these
reference indications within established limits. The fuel
system consists of the following components together
with interconnecting lines and fittings: a one gallon fuel
tank for fuel reserve during changeover from one
external fuel supply to another; a fuel float tank
incorporating a float switch which will initiate unit
shutdown to prevent damage to the fuel control in the
event the fuel supply is exhausted while the unit is
running; a manual push valve for purging from the fuel
float tank; an external fuel filter assembly; a fuel boost
pump to assure a constant inlet pressure to the fuel
control unit; a fuel filter assembly to filter fuel between
the fuel boost pump and fuel control unit; a manual push
valve for purging air from the fuel inlet system; a fuel
control unit to regular fuel flow to the combustion
chamber
in
response
to
engine
rpm
and
load
requirements; a fuel shutoff solenoid valve to provide
electrically actuated on and off control of fuel flow
between fuel control unit and fuel atomizer assembly; a
fuel atomizer assembly to provide a controlled fuel
spray
pattern
for
proper
fuel
combustion;
an
acceleration and overtemperature control thermostat to
prevent excessive exhaust gas temperature during
engine acceleration.
(d) Bleed-Air Control System fig 1-4). The bleed-air
control system automatically limits the amount of
compressed air available for external applications, thus
maintaining a safe engine operating temperature and
preventing an overload
Change 6
1-5
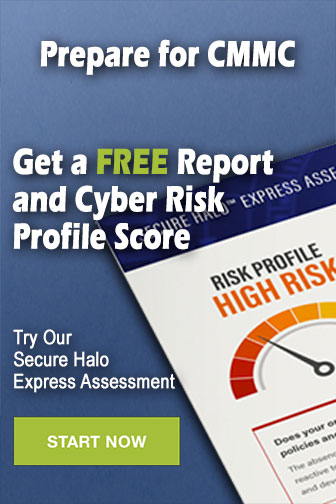