TM 5-6115-590-12
outlets of the power plant water system to other elements of the MUST system. The two hoses are heated by a
thermostatically controlled heater that is powered from the 400 Hz electrical system of the power plant.
b.
Inspection. Visually inspect the dual water hose assembly for damage, signs of leakage, stripped or crossed
threads on coupling nuts and electrical connectors, missing or damage protective cap or plugs.
(1) Test the heater by applying 400 Hz, 120 VAC. Connector pin arrangement is as follows: pin A; spare, pin
B; spare, pin C: 400 Hz, 120 VAC (phase!, pin D: 400 Hz, 120 VAC (neutral), pin E: ground.
(2) Test for leaks at 100 PSI water pressure.
c.
Replacement. The dual water hose assembly is replaced by simply disconnecting it from the hot and cold water
outlets.
4-21. Supply and Drain Water Hose Assembly.
a.
General. The supply and drain water hose assembly is used for connecting an external water source to the
power plant water system. The hose is heated by a thermostatically controlled heater that is powered by the 400 Hz
electrical system of the power plant.
b.
Inspection. Visually inspect hose assembly for damage, signs of leakage, stripped or crossed threads, missing or
damaged plugs or protective caps. Inspect heated flap of water recirculating hose assembly for visible damage.
(1) Test the heaters with 400 Hz, 120 VAC. Connector pin arrangement is: pin A, spare; pin B, spare; pin C,
400 Hz, 120 VAC; phase, pin D, 400 Hz, 120 VAC (neutral); pin E, ground.
(2) Test for leaks in hoses at 75 PSI water pressure.
c.
Replacement. The supply and drain water hose assembly is replaced by simply disconnecting it from the water
inlet and drain fittings.
4-22. Power Cable Assemblies, 60 and 400 Hz
a.
General. The 60 and 400 Hz power output cable assemblies (fig. 1-15, sheet 2 of 7) are used to connect the
power plants 60 and 400 Hz electrical generating systems to other elements of the MUST hospital.
WARNING
Make sure power plant is shut down prior to replacing cables.
b.
Replacement. To replace the 60 and 400 Hz power cable assemblies, disconnect and remove.
c.
Inspection. Visually inspect the cable assemblies for damaged connectors, connector covers, sleeves or cables.
If damage is evident notify general support maintenance for repair.
4-23. External Fuel Filter/Separator and Hose Assemblies
a.
Disassembly and Removal of Canister and Filter Element.
(1) Loosen nuts and washers (fig. 3-1) until each nut is flush with the end of bolt. Each bolt can then be
raised and rotated 180 degrees so the flanged portion of the bolt head is clear of cover.
(2) Remove cover and discard gasket. Remove screws, washers and the filter canister bracket assembly.
Then remove filter element from tank and remove aluminum plug.
(3) Remove canister from tank, then remove grommet and standpipe from the canister.
b.
Inspection. Inspect the filter/separator and the frame of the skid for damage to the extent that welding may be
required.
WARNING
All flammable vapors and excess fluid must be removed prior to cleaning or welding.
c.
Cleaning.
(1) Steam clean or wash all exterior surfaces of the filter/separator with a solution of 6 oz. of trisodium
phosphate, Specification 0-T-071, per gallon of water. After cleaning, rinse thoroughly and dry. Parts may be cleaned
more thoroughly by immersing or wiping with cleaning solvent, Federal Specification P-D-680.
WARNING
Dry cleaning solvent, P-D-680 or P-S-661 used to clean parts is potentially dangerous to personnel
and property. Avoid repeated and prolonged skin contact. Do not use near open flame or
excessive heat. Flash point of solvent is 100°F. (38"C).
d.
Welding and Repair. Welding to be performed by experienced aluminum welder only. Clean and prepare the
area requiring weld by the following methods in sequence.
(1) Chip out old weld or "V" out cracked area and stop drill if necessary.
(2) Wash and degrease area with deoxidizing agent and detergent to remove dirt, oil film and oxides.
(3) Brush with stainless steel wire brush until all foreign material is removed and metal becomes very bright.
e.
Assembly of Canister and Filter Element.
CAUTION
Make certain the grommet is properly seated around the canister. The grommet should cover the
mesh screen.
4-45
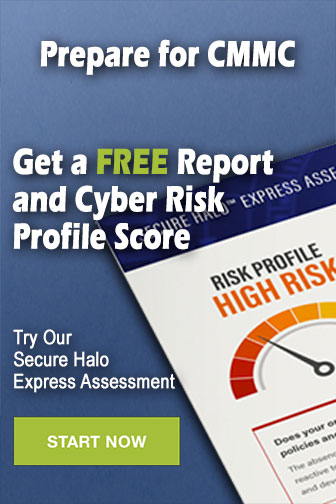