TM 5-6115-590-12
e. Adjustments.
(1) Acceleration and overtemperature control thermostat. If the acceleration and overtemperature control thermostat
is replaced, or if the controlling temperature is not as specified, check and adjust as follows.
(a) Connect gas turbine engine analyzer to power plant as described in paragraph 4-14b above except
paragraph 4-14b (6).
(b) Disconnect line from load control thermostat. Connect a control air plumbing line from the load control
thermostat line to the AIR IN fitting on the analyzer panel. Open needle valve on analyzer panel (fig. 4-14).
(c) Remove cap from acceleration limiter valve tee. Connect the 0-100 PSIG gauge set, provided with the
analyzer, to the open leg of the tee.
(d) Open conditioned air outlet compartment access door (fig. 1-2) and refrigeration compartment access
door (fig. 1-1).
(e) Start engine and accelerate to no load governed speed. Operate at this speed for approximately two
minutes to stabilize operation.
(f) Operate both heated air system at full heat as described in figure 2-16.
(g) With heated air systems operating at full heat, place the mode select switch to COOL on both systems.
The heated air flow control valves will remain open but the engine load control valve will close. Open the engine load
control valve by installing a jumper between analyzer jacks identified LOAD VALVE and DC POWER. This condition
bypasses the overtemperature thermoswitches in the air out compartment and delivers both cooled and heated air at the
same time to provide sufficient engine load to raise the exhaust gas temperature to 12400 to 12600F (6710C to 6820C)
for checking the thermostat setting.
CAUTION
Monitor the air out temperature and shut down the power plant if air discharge temperature
exceeds 200°F (93°C).
(h) With engine operating at full bleed load, slowly close needle valve (fig. 4-14) on gas turbine engine
analyzer panel until the AIR IN pressure indicator drops to approximately 14 psig. The exhaust gas temperature at which
engine speed and fuel pressure start to decrease is the acceleration and overtemperature control thermostat controlling
temperature.
CAUTION
Do not permit exhaust gas temperature to exceed 1260°F (682°C).
(i) If controlling temperature is not 1240F to 1260F (671C to 682C) shut down power plant and adjust
thermostat as follows.
(j) Remove thermostat by holding flats on thermostat valve (fig. 4-49) with a wrench and remove tube
assembly.
(k) Remove one attaching bolt and washer, retainer plate and shim washers. Remove thermostat from turbine
plenum flange. Remove thermostat valve from body.
(I) Measure total thickness of shims with micrometer. Add or remove shims as required. To decrease
temperature setting, increase shim stack thickness. To increase temperature setting decrease shim stack thickness. A
change of 0.001 inch in shim stack thickness will change controlling temperature by approximately 30
F. Install
corrected thickness of shims and fitting.
(m) Reinstall thermostat in reverse order of removal.
(n) Recheck controlling temperature at least twice. When controlling temperature is satisfactory, reconnect
load control thermostat line to load control valve. Disconnect and remove gas turbine engine analyzer.
(2) Load control thermostat. If the load control thermostat is replaced, or if the controlling temperature is not as
specified, check and adjust as follows.
(a) Connect gas turbine engine analyzer to power plant as described in paragraph 4-14b.
(b) Load engine as described in steps e.(1) (e), (f) and (g) above.
(c) Observe engine exhaust gas temperature on analyzer. The load control thermostat should modulate the
load control valve to control exhaust gas temperature at 1025F to 1075F (552C to 579C). If control temperature is
not 1025F to 1075F (552C to 579C), shut down power plant and adjust thermostat as follows.
(d) Remove thermostat by holding flats on thermostat valve with a wrench and remove tube assembly.
(e) Remove one attaching bolt and washer, retainer plate and shim washers. Remove thermostat from turbine
plenum flange. Remove thermostat valve from body.
(f) Measure total thickness of shims with micrometer. To decrease temperature setting, increase shim stack
thickness. To increase temperature setting, decrease shim stack thickness. A change of 0.001 in shim stack thickness
will change cracking temperature by approximately 30F. Add or remove shims as required. Install correct thickness of
shims and fitting.
(g) Reinstall thermostat in reverse order of removal.
(h) Recheck controlling temperature at least twice.
(i) When controlling temperature is satis
4-42
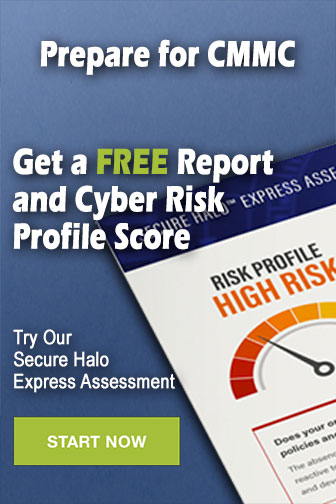